The Electric Vehicle Revolution and the Role of Batteries
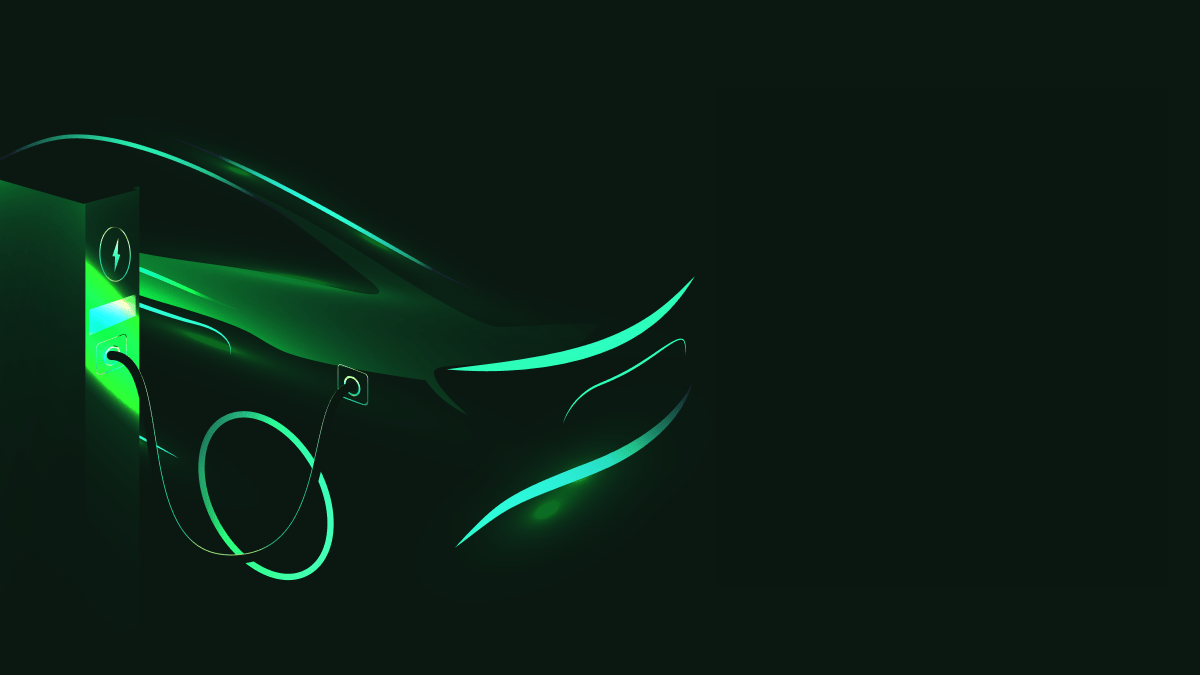
India’s automotive landscape is undergoing a rapid transformation, driven by factors such as government initiatives, technological advancements, and a growing environmental consciousness, with the electric vehicle (EV) industry at its core. Among the key drivers of this revolution is the battery.
We’ll delve into the evolution of lithium-ion batteries, exploring their origins, the crucial domain of mineral extraction, and the intricate manufacturing processes shaping the EV supply chain.
The Evolution of Lithium-ion Batteries:
Originally designed for laptops and consumer electronics, lithium-ion batteries have become frontrunners in the EV realm, thanks to their high energy density and extended cycle life. The journey traces back to the 1970s during an oil crisis when efforts to create a battery for clean energy solutions began. Breakthroughs by researchers like John B. Goodenough and Akira Yoshino led to the birth of the first lithium-ion battery. We’ll focus on two variants: Lithium Iron Phosphate (LFP) and Lithium Nickel Manganese Cobalt Oxide (LiNMC), each offering unique advantages. LFP batteries shine in cycle life, cost efficiency, temperature performance, and environmental impact. Meanwhile, LiNMC batteries boast higher energy density, positioning them as ideal for applications demanding increased power output and extended runtimes.
Mineral Extraction and Processing
There are several critical minerals required to manufacture the two variants discussed in this article. Like, Lithium, Nickel, Cobalt, Manganese, and Graphite among others.
When it comes to mining, China and the Democratic Republic of Congo (DRC) take the lead, followed by Australia and Indonesia (refer to the graph above). Cobalt, a crucial component, is primarily mined in the DRC, where approximately 75% of the world’s cobalt originates. China’s influence extends to the graphite supply chain, boasting the world’s highest natural graphite reserves and maintaining a commanding 99% control over spherical graphite production—a vital intermediate processing phase.
While Indonesia contributes about 40% of the world’s total nickel production, only a fraction is currently utilized in the electric vehicle (EV) battery supply chain. The primary Class 1 battery-grade nickel producers are Russia, Canada, and Australia.

Notes: Li = lithium; Ni = nickel; Co = cobalt; Gr = graphite; DRC = Democratic Republic of Congo. Geographical breakdown refers to the country where the production occurs. Mining is based on production data. Material processing is based on refining production capacity data. Cell component production is based on cathode and anode material production capacity data. Battery cell production is based on battery cell production capacity data. EV production is based on EV production data.
The graph above also shows how China currently holds sway over mineral processing, refining over 50% of the minerals crucial for batteries, including lithium, cobalt, graphite, and manganese – that’s 3 out of 4 of the important minerals required to make a battery.
It is crucial to note that, despite global plans for widespread EV adoption, only a few countries possess reserves of these critical minerals, and fewer still mine & process the reserves. It is essential to acknowledge potential challenges and risks associated with this concentration. For example, cobalt extraction in the Democratic Republic of Congo (DRC), often conducted with basic tools in manual excavation efforts, raises questions about worker safety and ethical mining practices. Geopolitical risks, such as trade tensions or supply chain disruptions, could impact the stability of the battery supply chain.
Discovering Lithium Reserves in India
The Geological Survey of India (GSI) has identified Lithium reserves in Jammu & Kashmir, Rajasthan, Karnataka, and Jharkhand. Jammu and Kashmir’s reserve of 5.9 million tonnes ranks as the world’s seventh-largest reserve. Rajasthan’s discovery could potentially meet 80 percent of India’s lithium demand, reducing dependency on China.
Understanding the Concentration in Lithium-ion Battery Production
A Lithium-ion battery cell consists of essential components: a cathode, anode, cell separator, and cell electrolyte, each playing a crucial role. The subsequent stages involve cell assembly and pack assembly, ultimately resulting in the final battery.
Cathode and anode production are highly concentrated globally, mainly controlled by a few companies. Seven companies, for instance, make up 55% of the global cathode capacity. China leads in cathode production with a significant 70%, while Korea and Japan trail at 15% and 14%, respectively. Anode production is even more centralized, with China dominating at 85%. Japan contributes 11%, and Korea holds a 3% share. Notably, only four companies produce over 50% of the global anode capacity.
Cost breakdown
The cost breakdown reveals that the manufacturing of these four essential components accounts for a substantial 69% of the total battery cost, with an additional 27% allocated to cell assembly. Currently, India heavily relies on imports, with 96% of the total battery cost spent on imported components. A meager 4% of the cost is domestically handled via pack assembly. To enhance self-reliance and exert control, India must progress towards assembling battery cells domestically—a crucial step in building capabilities for the entire battery manufacturing process. Hence, controlling over 30% of the cost (see table below for detailed breakup).
Manufacturing segments | Component value for LFP (in total battery Cost) | Component value for NMC 532 (in total battery Cost) |
Cell cathode: The cathode is the electrode in a battery cell where reduction takes place during discharge | 30% | 54% |
Cell anode: The anode is the electrode in a battery cell where oxidation takes place during discharge | 21% | 14% |
Cell separator: A membrane that separates the anode and cathode in a battery cell, allowing the flow of ions while preventing the electrodes from touching. | 8% | 5% |
Cell electrolyte: A substance (usually a liquid or gel) in a battery cell that conducts ions between the anode and cathode, completing the circuit and generating an electric current. | 10% | 6% |
Cell assembly: Cell assembly is the process of assembling the anode, cathode, separator, and electrolyte to create a complete battery cell. | 27% | 17% |
Pack assembly: Pack assembly is the process of assembling multiple battery cells into a larger battery pack or module for use in applications such as EVs or grid storage. | 4% | 4% |
India’s Ambitious EV Targets and Rapid Adoption Growth
India has set ambitious goals for electric vehicle (EV) adoption, aiming for 80% of two-wheeler and three-wheeler vehicles, 70% of commercial cars, 40% of buses, and 30% of private car sales to be electric by 2030.
Insights from the IISD report highlight challenges and opportunities in the battery supply chain, emphasizing government initiatives like the Production Linked Incentive for Advanced Chemistry Cell (PLI-ACC) scheme. This move not only brings cell manufacturing to the forefront but also signals support for private capital crucial to the EV battery value chain.
Corporate Decision-Making in the Evolving EV Supply Chain
In assessing the factors influencing corporate decision-making in the electric vehicle (EV) and battery industries, India emerges as a compelling investment destination. An expansive market potential is a primary driver, underpinned by the government’s ambitious targets and initiatives. The commitment to cultivating a conducive ecosystem positions India favorably for companies seeking assured demand. Moreover, India’s strategic emphasis on the entire battery supply chain, particularly mineral processing, underscores its dedication to building a robust local ecosystem and reducing reliance on imports.
India’s appeal is further strengthened by its well-developed transport infrastructure and strategic port locations, positioning it as an attractive hub for EV and battery manufacturing. Additionally, India’s competitive advantage in labor costs, coupled with state-level subsidies and supportive policies, positions the country as an attractive destination for companies seeking access to cost-effective and skilled labor. Nevertheless, challenges such as land acquisition and the need for clearer regulations on inputs, technology, and environmental considerations highlight areas for improvement to enhance India’s competitiveness.
Conclusion: Charting the Course for India’s EV Odyssey
As India propels itself toward an electric future, the symbiotic relationship between battery technology, EV manufacturing, and government initiatives becomes increasingly apparent. The Electric Mobility smallcase, reflecting companies deeply invested in the electric vehicle ecosystem, mirror the broader trend toward a greener, more sustainable transportation landscape. The collaborative efforts of the private sector and government initiatives set the stage for India’s ascent as a significant player in the global electric mobility arena.
Explore Electric Mobility smallcase
Disclaimer: Investment in securities market are subject to market risks. Read all the related documents carefully before investing. Registration granted by SEBI, membership of BASL and certification from NISM in no way guarantee performance of the intermediary or provide any assurance of returns to investors. The content in these posts/articles is for informational and educational purposes only and should not be construed as professional financial advice and nor to be construed as an offer to buy/sell or the solicitation of an offer to buy/sell any security or financial products. Users must make their own investment decisions based on their specific investment objective and financial position and use such independent advisors as they believe necessary. Refer to our disclosures page, here. Windmill Capital Private Limited – Research Analyst – SEBI reg. no: INH200007645; Compliance Officer – Ajoy Bharadwaj, Phone Number – 8296014433; Email Id – compliance@windmill.capital; Support email id – notifications@windmill.capital